The Significance of Precision Molds in Metal Fabrication
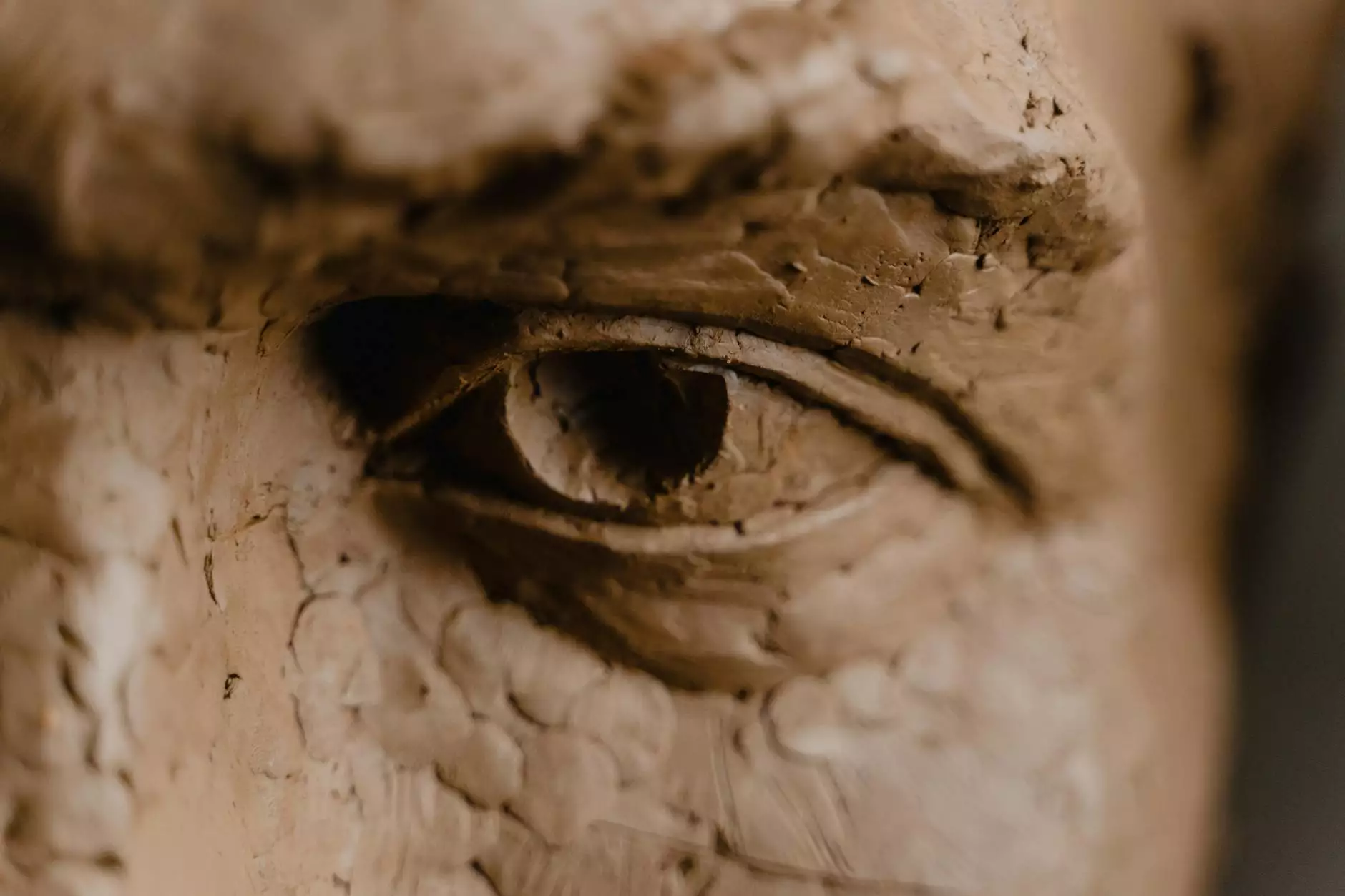
In today's competitive manufacturing landscape, the role of precision molds has become increasingly crucial. As industries evolve, the demand for parts that exhibit high precision and quality is paramount. This article delves into the various dimensions of precision molds in the field of metal fabrication, highlighting their importance, applications, and benefits.
Understanding Precision Molds
Precision molds are tools used to shape materials into desired forms with high accuracy and minimal tolerance for error. They are essential in producing components for various industries such as automotive, aerospace, electronics, and consumer goods. By utilizing advanced technology and methods, manufacturers create molds that enhance the efficiency and quality of the fabrication process.
The Importance of Precision in Manufacturing
Precision in manufacturing is not merely a preference—it is a necessity. Here are several reasons why precision is critical:
- Quality Assurance: Higher precision guarantees superior quality of the output, reducing the likelihood of defects.
- Cost Efficiency: With precise molds, less material waste occurs, leading to reduced production costs over time.
- Shorter Lead Times: Precision molds enable faster production, which is vital for keeping up with market demands.
- Enhanced Performance: Parts that are made with precision molds typically perform better in their respective applications.
How Precision Molds are Manufactured
The manufacturing process for precision molds is highly specialized and requires advanced technology and skilled craftsmanship. The following steps outline the typical process:
1. Design Process
The journey begins with designing the mold using CAD (Computer-Aided Design) software. This stage includes:
- Conceptualization: Developers and engineers collaborate to define the required specifications.
- 3D Modeling: A detailed digital model of the mold is created, allowing for adjustments before production.
2. Material Selection
Choosing the right material is crucial for the durability and effectiveness of the mold. Common materials include:
- Steel: Known for its toughness and longevity.
- Aluminum: Lightweight and easy to work with, suitable for prototypes.
- Copper: Excellent for thermal conductivity, often used in high-precision applications.
3. Machining
Once the design is finalized and materials selected, the machining process begins. This involves various techniques such as:
- Milling: Removing material to shape the mold.
- EDM (Electrical Discharge Machining): Used for intricate details that require extreme precision.
- Grinding: Final finishing to achieve the desired surface quality.
Applications of Precision Molds
Precision molds find applications across a multitude of industries. Here are some notable examples:
1. Automotive Industry
The automotive sector relies heavily on precision molds for manufacturing parts such as:
- Engine Components: Ensuring perfect fit and functionality.
- Body Panels: Providing both aesthetics and safety features.
2. Aerospace Engineering
In aerospace, the performance and safety of components are critical. Precision molds are used to create:
- Engine Parts: High-resistance components must withstand extreme conditions.
- Structure Components: Lightweight yet strong elements that contribute to overall performance.
3. Electronics Manufacturing
Precision molds also play an essential role in electronics, where parts must fit together with minimal tolerance. Common applications include:
- Casings: Protective outer layers for devices.
- Connectors: Ensuring electrical components function smoothly.
Benefits of Using Precision Molds
Utilizing precision molds offers numerous benefits, which can enhance productivity and profitability in manufacturing:
- Increased Efficiency: Precision molds contribute to streamlined production processes, reducing cycle times.
- Reduced Waste: Higher accuracy means less material is wasted during production.
- Cost-Effectiveness: Although initial costs may be higher, the long-term savings on material and labor make precision molds an economical choice.
- Consistency: Precision molds produce uniform parts, allowing for extensive scaling without compromising quality.
Choosing the Right Manufacturer for Precision Molds
Selecting a manufacturer for your precision mold needs is a critical decision that can affect the success of your project. Here are key factors to consider:
1. Expertise and Experience
Look for a manufacturer with a proven track record in making precision molds. Experience in various industries can also be beneficial.
2. Advanced Technology
Utilizing state-of-the-art machinery and software is essential for crafting high-quality molds. Ensure that the manufacturer stays updated with technological advancements.
3. Quality Assurance
A reputable manufacturer should have rigorous quality control processes in place. Certifications such as ISO can indicate adherence to high standards.
4. Customer Support
Effective communication and support can make a difference in the overall manufacturing experience. Choose a partner that is responsive to your queries and needs.
Future Trends in Precision Molds
The future of precision molds is shaped by constant advancements in technology and manufacturing processes. Here are a few trends to watch out for:
1. Additive Manufacturing
This innovative approach will likely become prominent in mold design, allowing for more complex shapes and reduced lead times.
2. Smart Molding Technologies
Incorporating IoT (Internet of Things) devices into mold-making processes allows for real-time monitoring and optimization of production.
3. Sustainable Practices
As industries shift towards sustainability, the demand for eco-friendly materials and processes in mold manufacturing will grow.
Conclusion
In summary, precision molds are indispensable in the realm of metal fabrication. From enhancing quality to reducing costs, the role they play is critical for manufacturers aiming for excellence. By understanding the importance, applications, and modern trends surrounding precision molds, businesses can make informed decisions that contribute to their success.
If you are looking for a reliable partner in precision mold manufacturing, consider reaching out to experienced professionals like those at DeepMould.net to ensure your production needs are efficiently met.