The Ultimate Guide to Die Casting Parts Supplier Services
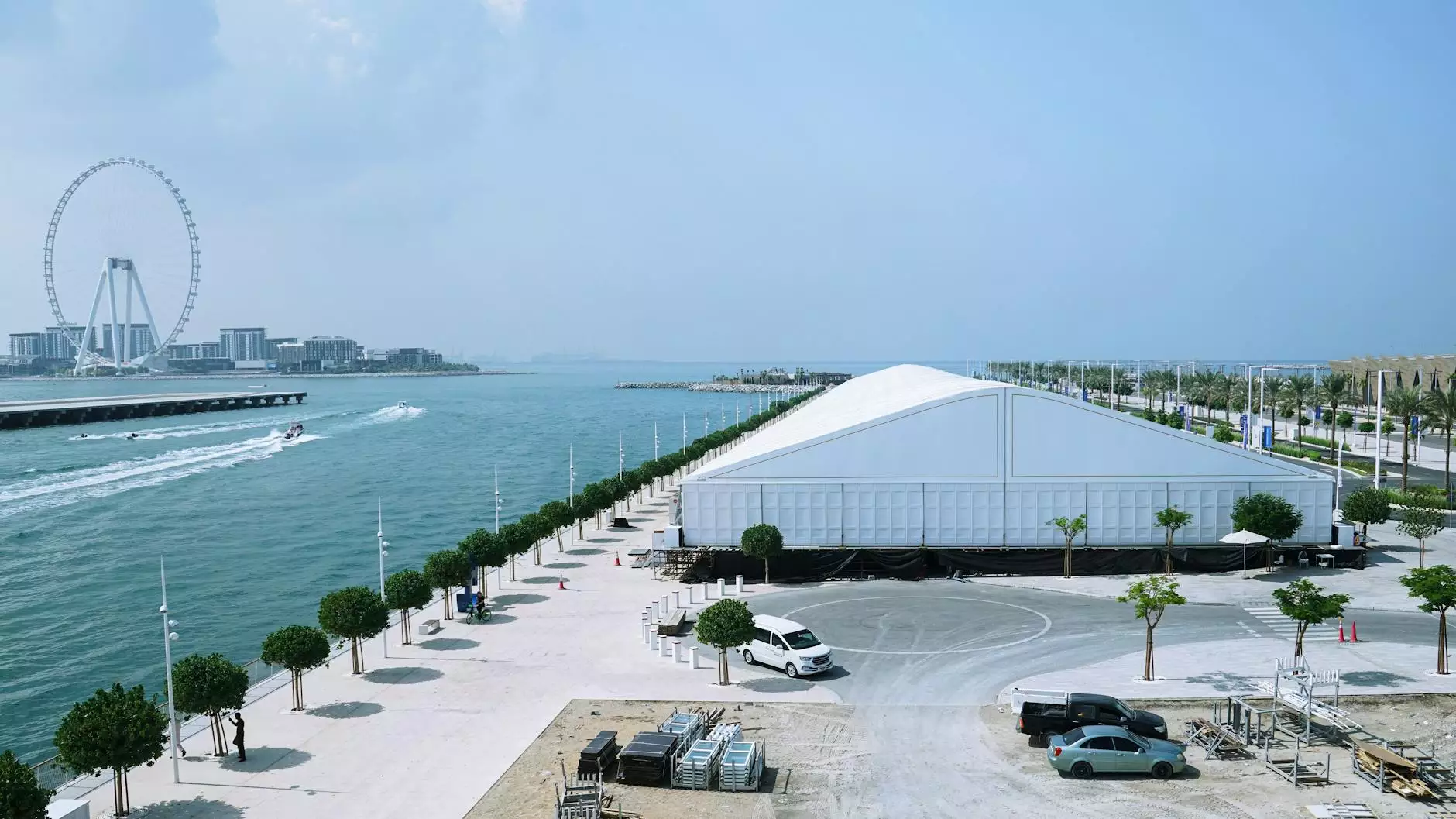
In the fast-evolving world of manufacturing, finding a reliable die casting parts supplier has become paramount. Industries are constantly in need of high-quality parts that not only meet their specifications but also enhance their overall production efficiency. This comprehensive guide provides insight into the intricate world of die casting and how partnering with the right supplier can lead to significant operational benefits.
Understanding Die Casting
Die casting is a precision manufacturing process that allows for the creation of intricate shapes and designs using metal. The process involves forcing molten metal into a mold cavity under high pressure, which results in parts that exhibit excellent dimensional accuracy and smooth surface finishes.
Key Benefits of Die Casting
- High Precision and Detail: Die casting produces parts with complex geometries that require minimal post-processing.
- Strong and Durable Parts: The resulting components are robust and can withstand significant wear and tear.
- Efficiency in Production: High production rates are achievable, making it suitable for mass production.
- Material Versatility: Various alloys, including aluminum, zinc, and magnesium, can be used based on the application demands.
Selecting the Right Die Casting Parts Supplier
With a plethora of options available, selecting the right die casting parts supplier can be overwhelming. Here are crucial factors to consider when making your choice:
1. Experience and Expertise
Evaluate the supplier's track record in the industry. A supplier with extensive experience will be more adept at understanding your project's unique requirements and challenges.
2. Quality Assurance Processes
Ensure that the supplier adheres to rigorous quality control standards. This includes the certifications that affirm their commitment to quality, such as ISO certifications. High-quality parts are essential for maintaining the integrity of your final products.
3. Range of Services Offered
Some suppliers offer additional services that can be beneficial, such as design assistance, prototyping, finishing options, and assembly. A manufacturing partner who can provide comprehensive solutions will add significant value to your operations.
4. Technological Capabilities
Investigate the technological advancements the supplier utilizes in their die casting process. Suppliers that employ modern technologies such as automated die casting systems will often produce superior results with greater efficiency.
5. Customer Service and Support
Look for a supplier that values customer relationships and offers responsive support. Communication is key to a successful partnership, especially when addressing concerns or modifications during the production process.
Why Choose DeepMould as Your Die Casting Parts Supplier
At DeepMould.net, we pride ourselves on being a top-tier die casting parts supplier dedicated to excellence. Our commitment to quality, innovation, and customer satisfaction sets us apart in the competitive landscape of metal fabrication services.
Unmatched Quality
This is at the heart of everything we do. Our state-of-the-art facilities and stringent quality control measures ensure that every part we manufacture meets the highest standards. We specialize in innovative die casting techniques that facilitate the production of complex components with precision.
Innovative Solutions Tailored to Your Needs
We understand that every project is unique. That’s why our team of experts works closely with you to develop customized solutions that align with your specific requirements. Whether it’s a small batch or a large production run, we have the capability to meet your needs efficiently.
Comprehensive Support and Consultation
From the initial design phase through to final delivery, our dedicated team provides ongoing support and consultation. We believe in fostering strong relationships with our clients and providing clear communication at every step, ensuring that your project runs smoothly.
Commitment to Sustainability
As a responsible manufacturer, we are committed to sustainable practices. We continuously strive to minimize waste and maximize energy efficiency in our operations. Partnering with us means you’re also contributing to environmentally friendly practices in manufacturing.
The Die Casting Process: A Detailed Overview
Understanding the die casting process is vital for any business looking to utilize this method of manufacturing. Here's a step-by-step breakdown:
1. Mold Preparation
The first step in the die casting process is preparing the mold. Molds are often made from steel due to its longevity and ability to withstand high pressures. The design of the mold is crucial and should accommodate the thermal expansion of the metal.
2. Metal Melting
The metal, typically an alloy, is heated to its melting point in a furnace. This process needs to be carefully controlled to ensure the metal remains within the specified temperature range, preventing defects in the final product.
3. Injection of Molten Metal
Once melted, the molten metal is injected into the mold at high pressure, ensuring it fills even the most intricate designs. This rapid injection is key to achieving the fine details necessary for modern applications.
4. Cooling and Solidification
After injection, the metal must cool and solidify within the mold. The cooling time depends on the intricacies of the part and the metal used. Once cooled, the mold is opened, and the finished part is expelled.
5. Finishing Processes
Post-casting processes such as machining, painting, or surface treatment are often required to meet final specifications and enhance appearance. These steps can significantly improve the functionality and aesthetics of the parts.
Applications of Die Cast Parts
Die casting finds use in diverse industries due to its ability to produce strong, lightweight components. Here are some notable applications:
- Automotive Industry: Components such as engine blocks, transmission housings, and brackets.
- Electronics: Housings for electronic devices and components requiring high precision.
- Consumer Products: Various parts for appliances, tools, and furniture.
- Aerospace: Critical components where weight and strength are paramount.
Conclusion
In conclusion, selecting the right die casting parts supplier can significantly impact your business's operational success and product quality. With DeepMould.net, you gain a partner that is committed to providing exceptional quality, innovative solutions, and unparalleled support. By leveraging our expertise, businesses can enhance their production capabilities and stay competitive in an ever-evolving market. Choosing DeepMould isn’t just a decision; it’s a step towards excellence in manufacturing.
Contact Us for Your Die Casting Needs
If you are in search of a proficient die casting parts supplier, look no further than DeepMould. Contact us today to discuss your project requirements and discover how we can assist in bringing your vision to life!